The Evolution of Operational Data

When I started my career in Automation, the industry was getting used to the idea of extracting data from automation systems and using this for reporting purposes. This was to avoid having to manually capture readings from various pieces of equipment from around the plant at regular intervals.
Retrospective Data
Organizations relied on data at the end of each shift or batch to evaluate the progress and efficiency of their operations. These readings were then used to perform calculations based on what was recorded in the previous shift.
By that stage, this information presented no more than a post-mortem of events that had taken place, which could then in turn be used to help improve the next cycle.
If a fault had occurred, the information could also help to try and understand the cause of the failure.
Reporting Tools
One of my first jobs in industrial automation involved developing a system for Sydney Water where I used SQL commands to get meter readings from the control system. Once I had the readings I would then write the data into MS Excel and Access (which at the time felt very cutting edge!). This was the main driver for the introduction of reporting tools. Customers wanted to avoid human error caused by taking these repetitive readings and required reports to be automated.
Industrial Internet of Things (IIOT)
With the evolution in smart devices and access to real-time data, it became easier to make accurate and informed decisions regarding operations based on what was happening on the plant in real-time.
However, if a failure occurred, downtime was inevitable. For many processes any unplanned downtime could prove detrimental to equipment health and be extremely costly. Some processes require a complete restart resulting in many days of subsequent downtime and costing huge amounts in lost revenue.
Predictive Analytics
The onset of IIOT and industry 4.0 led to the end consumer being flooded with information coming from devices that are smarter than ever. Moreover, we are evolving towards self-optimizing autonomous systems that could further lead to information overload.
Organisations can now change their course of action based on what is likely to happen.
Predictive analytics systems actively predict when a fault is likely to occur based on historical behaviours and patterns of equipment and processes. This allows operations to plan their downtime, and maintenance cycles and avoid damaging their valuable assets.
The immense amount of data availability is one of the real values unlocked through the emergence of IIOT.
The immense amount of data availability is one of the real values unlocked through the emergence of IIOT.
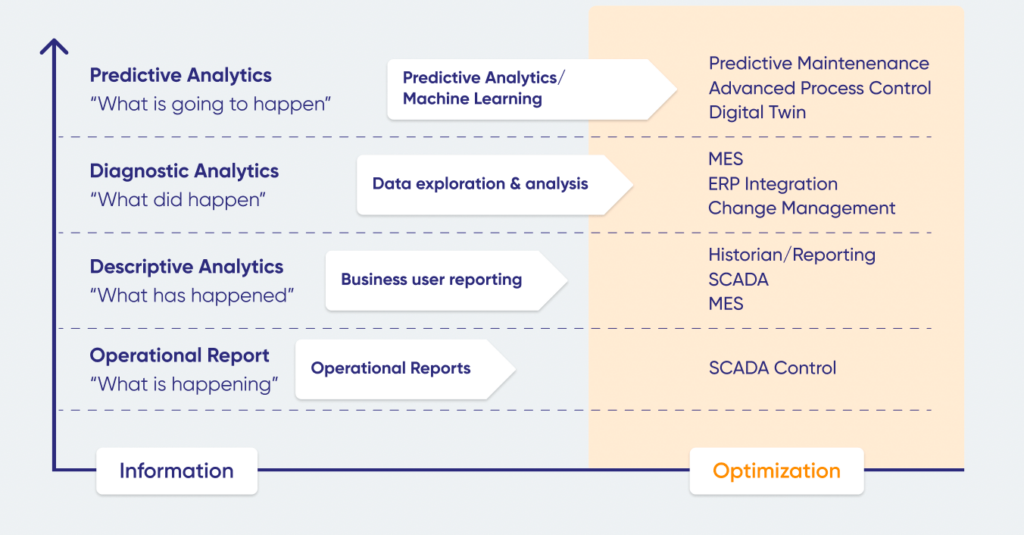
The IT and OT divide
Another byproduct of this data availability is the convergence of the IT and OT space. This convergence has allowed for the interoperability of the automation systems with the rest of the organisation’s business systems be it maintenance, ordering or ERP.
What happens on the plant can now autonomously adjust the course of the entire supply chain to minimise impact on the bottom.
These systems are no longer just interacting within the operational environment. They are now working together with the organisation’s business decision making tools to further enrich the decision making process.
This information is vital for informed and intelligent decision making – a requisite in today’s competitive marketplace.
This information is vital for informed and intelligent decision making – a requisite in today’s competitive marketplace.
Want to know more about future-proofing your operations and getting the most out of your existing automation assets?
Speak to one of our specialised consultants on how we can help your organisation on its transformational journey towards efficiency and transparency.